All blog posts
Explore the world of design and learn how to create visually stunning artwork.
Which HAZWOPER Training Do You Need? (Different Levels)
November 14, 2023 | by onlineoshasafetytraining.com
Is In-Person Hazwoper Training Right for You? (Pros & Cons)
November 14, 2023 | by onlineoshasafetytraining.com
Where Can You Get Free HAZWOPER Training? (5 Ways)
November 14, 2023 | by onlineoshasafetytraining.com
How to Get HAZWOPER Certified in 2024? (Step-by-Step)
November 14, 2023 | by onlineoshasafetytraining.com
Does HAZWOPER Certification Expire? (Get Refresher Course Now)
November 14, 2023 | by onlineoshasafetytraining.com
How to Take the Hazwoper Training for New Employees?
November 14, 2023 | by onlineoshasafetytraining.com
HAZWOPER Training for Healthcare Professionals
November 14, 2023 | by onlineoshasafetytraining.com
How to Choose the Best HAZWOPER Training Programs?
November 13, 2023 | by onlineoshasafetytraining.com
HAZWOPER Training Grants & Funding: How to Avail
November 13, 2023 | by onlineoshasafetytraining.com
Custom HAZWOPER Training for Companies: The Right Approach
November 13, 2023 | by onlineoshasafetytraining.com
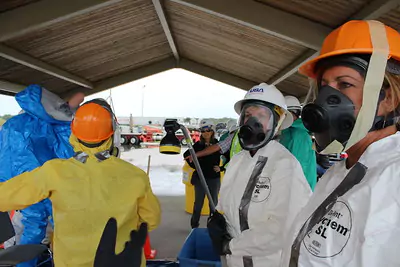
To determine the appropriate HAZWOPER training, you need to consider several factors based on the Occupational Safety and Health Administration (OSHA) guidelines. The level of training required depends on the specific role and responsibilities of the individual, as well as the types of hazards they might encounter. Here are the key types of HAZWOPER training:
- 40-Hour HAZWOPER Training: This is designed for workers involved in cleanup operations, voluntary clean-up operations, emergency response operations, and storage, disposal, or treatment of hazardous substances or uncontrolled hazardous waste sites. It’s comprehensive training for workers who deal with hazardous substances regularly.
- 24-Hour HAZWOPER Training: This is for workers on a site only occasionally for a specific limited task (such as, but not limited to, ground-water monitoring, land surveying, or geophysical surveying) and who are unlikely to be exposed over permissible exposure limits and published exposure limits.
- HAZWOPER 8-Hour Annual Refresher Course: This is a yearly refresher course required for maintaining the 40-hour or 24-hour HAZWOPER certification. It’s designed to update workers on new technologies, methods, and regulations related to hazardous waste operations and emergency response.
- HAZWOPER 8-Hour Supervisor Training: This is for workers who are already 40-hour or 24-hour certified and are taking on managerial or supervisory roles on hazardous waste operations sites.
- Emergency Response Operations Level Training: This varies depending on the role in emergency response, such as First Responder Awareness Level, First Responder Operations Level, Hazardous Materials Technician, Hazardous Materials Specialist, and On-Scene Incident Commander. Each level has specific training requirements based on the complexity of the role and the degree of hazard exposure.
Choosing the right HAZWOPER training involves assessing the specific work environment, the frequency and nature of contact with hazardous substances, and the level of responsibility in handling or responding to hazardous situations. Compliance with OSHA’s HAZWOPER standard (29 CFR 1910.120) is crucial for worker safety and environmental protection.
Read related article: Is In-Person Hazwoper Training Right for You? (Pros & Cons)
Understanding Different Levels of HAZWOPER Training
A. 40-Hour HAZWOPER Training
- Target Audience and Applicability
- Designed for workers involved in the clean-up, emergency response, and treatment or storage of hazardous waste.
- Applicable to those who will potentially be exposed to hazardous substances.
- Key Components and Topics Covered
- Training covers a variety of topics including hazard recognition, chemical and physical properties of hazardous substances, protective equipment usage, decontamination procedures, and emergency response.
- Focus on safety and health procedures, including hands-on experience with equipment and simulated scenarios.
- Scenarios Requiring 40-hour Training
- Required for workers at uncontrolled hazardous waste sites, such as EPA Superfund sites.
- Necessary for individuals participating in voluntary clean-up operations and emergency response activities involving hazardous waste.
B. 24-Hour HAZWOPER Training
- Description and Intended Audience
- Intended for workers who visit hazardous waste sites occasionally and are unlikely to be exposed to hazardous substances above permissible levels.
- Suitable for those involved in specific tasks like surveying, logging, or sampling.
- Overview of Curriculum
- Focuses on recognizing and avoiding hazards, understanding regulatory requirements, and basic response procedures.
- Less in-depth than the 40-hour course but still covers essential safety protocols.
- Situations Where 24-hour Training is Sufficient
- Appropriate for workers who have limited exposure to hazardous sites, such as engineers, surveyors, or administrative personnel.
- Suitable for those who are on-site occasionally but not involved in cleanup or emergency response.
C. HAZWOPER 8-Hour Annual Refresher Course
- Purpose and Necessity
- Designed to maintain the skills and knowledge acquired in the 40-hour or 24-hour training.
- Mandatory for keeping HAZWOPER certification current and compliant with OSHA regulations.
- Content Typically Reviewed in the Refresher
- Updates on regulatory changes, new technologies, and best practices in hazardous waste operations.
- Review of safety protocols, emergency response procedures, and personal protective equipment usage.
- Compliance and Regulatory Aspects
- Required annually to comply with OSHA’s HAZWOPER standard (29 CFR 1910.120).
- Ensures workers are up-to-date with the latest safety guidelines and industry standards.
D. HAZWOPER 8-Hour Supervisor Training
- Significance for Managers and Supervisors
- Tailored for individuals who oversee hazardous waste operations, ensuring they can manage safety and health risks effectively.
- Emphasizes leadership roles in hazardous environments and the responsibility for worker safety.
- Leadership and Safety Management Topics
- Covers topics such as risk assessment, incident command system, and effective communication during emergencies.
- Focuses on developing leadership skills to maintain safety standards and ensure compliance.
- Implementation of Safety Protocols at the Supervisory Level
- Supervisors learn to implement and monitor safety protocols, conduct safety briefings, and manage emergency response.
- Responsible for ensuring their team adheres to safety practices and regulatory requirements.
Read related article: Where Can You Get Free HAZWOPER Training?
Industry-Specific HAZWOPER Training Requirements
1. Chemical Manufacturing Industry:
- OSHA 29 CFR 1910.120(e)(3)(i): This regulation mandates a minimum of 24 hours of training for employees in the chemical manufacturing sector, with an emphasis on handling hazardous waste and emergency response.
- Process Safety Management (PSM) Integration: Training incorporates elements of PSM (29 CFR 1910.119), focusing on understanding and controlling chemical hazards during processing.
- Chemical-Specific Hazard Communication: Detailed instruction on Globally Harmonized System (GHS) for chemical classification, labeling, and Safety Data Sheets (SDS).
2. Oil and Gas Industry:
- Emergency Response Preparedness: Tailored training for oil spill response, well blowout control, and natural gas leak management. Incorporation of Incident Command System (ICS) protocols for large-scale incidents.
- Confined Space Entry Regulations (29 CFR 1910.146): Specialized training for workers entering confined spaces, such as tanks and vessels, focusing on atmospheric testing and non-entry rescue techniques.
- Hydrogen Sulfide (H2S) Awareness: Training in detecting and responding to H2S, a common toxic gas in the oil and gas industry, including the use of personal gas detectors and emergency breathing systems.
3. Pharmaceutical Industry:
- Biological Hazard Management: Training in handling biohazardous materials, including containment and decontamination procedures, aligned with Biosafety Level (BSL) requirements.
- Cleanroom Operations: Specialized training for working in controlled environments, focusing on contamination control, proper gowning techniques, and cleanroom behavior protocols.
4. Waste Treatment and Disposal Industry:
- RCRA (Resource Conservation and Recovery Act) Compliance: Training in hazardous waste management as per EPA regulations (40 CFR 260-280), focusing on waste characterization, segregation, and disposal techniques.
- Landfill Operations Safety: Training on safe operations in landfill environments, including leachate management and methane monitoring.
5. Construction Industry (Environmental Remediation Projects):
- Asbestos and Lead Abatement: Specific training for handling asbestos and lead, focusing on exposure limits (OSHA 29 CFR 1926.1101 for asbestos, 29 CFR 1926.62 for lead), PPE requirements, and air monitoring protocols.
- Soil and Groundwater Contamination: Training in remediation techniques, including excavation safety, soil sampling, and groundwater treatment methods.
Industry-specific HAZWOPER training requirements vary significantly, with a focus on the unique hazards and operational contexts of each industry. The training combines regulatory compliance (OSHA, EPA standards) with practical skills and emergency response procedures, tailored to the specific needs of different industry sectors. This specialized approach ensures that workers are equipped with the necessary knowledge and skills to safely handle hazardous materials and respond to emergencies in their respective fields.
Read related article: Custom HAZWOPER Training for Companies: The Right Approach
Specialized Emergency Response Training Levels
A. First Responder Awareness Level
- Description
- This level is for individuals who are likely to witness or discover a hazardous substance release and are trained to initiate an emergency response sequence by notifying proper authorities.
- Responsibilities and Required Competencies
- Recognize the presence of hazardous substances, understand the risks, and secure the area.
- Not expected to participate in the actual containment or control of the spill.
- Training Requirements and Certifications
- Basic training focusing on recognizing hazardous substances and understanding their risks.
- No hands-on engagement with the hazard; emphasis on communication and safety protocols.
B. First Responder Operations Level
- Description
- Personnel at this level respond to releases or potential releases to protect nearby persons, property, or the environment from the effects of the release.
- Responsibilities and Required Competencies
- Knowledgeable in hazard and risk assessment, basic control, containment, and/or confinement operations.
- Understand decontamination procedures and standard operating procedures for emergency response.
- Training Requirements and Certifications
- More advanced than the awareness level, focusing on defensive operations.
- Typically requires a specific number of training hours as per OSHA standards.
C. Hazardous Materials Technician
- Description
- Technicians are individuals who respond to hazardous substances to stop the release actively.
- Responsibilities and Required Competencies
- Must demonstrate a more comprehensive understanding of hazardous materials and the associated risks.
- Skilled in using advanced protective gear, technical equipment, and containment methods.
- Training Requirements and Certifications
- Extensive training in the areas of hazard recognition, equipment use, and containment techniques.
- Certification often requires completing a specified course and passing practical and written exams.
D. Hazardous Materials Specialist
- Description
- Specialists have a more in-depth knowledge of specific hazardous substances and act as a support role for the hazardous materials technician.
- Responsibilities and Required Competencies
- Provide expertise on handling hazardous substances, including assessment and advice on decontamination.
- Serve as a liaison with federal, state, local, and other government officials in regards to hazardous materials.
- Training Requirements and Certifications
- Requires comprehensive training, often building on the hazardous materials technician training.
- In-depth knowledge of various hazardous substances and emergency response protocols.
E. On-Scene Incident Commander
- Description
- Individuals who assume control of the incident scene beyond the first responder level.
- Responsibilities and Required Competencies
- Responsible for all aspects of the response, including developing strategies, tactics, and safety measures.
- Require leadership abilities, decision-making skills, and comprehensive knowledge of hazardous materials management.
- Training Requirements and Certifications
- Advanced training in incident command and control, operational planning, and resource management.
- Certification typically involves extensive experience and training in hazardous materials response and management.
Read related article: HAZWOPER 40-hour Course Schedule (The Typical 5-Day Plan)
Specialty Emergency Response Training
A. Distinction Between First Responder Awareness and Operations Levels
- First Responder Awareness Level
- Focuses on recognizing the presence of hazardous materials and initiating the proper emergency response.
- Emphasizes risk assessment, securing the area, and communication with relevant authorities.
- First Responder Operations Level
- Trains responders to act defensively to protect people, property, and the environment.
- Involves understanding basic hazard and risk assessment techniques and how to contain the release from a safe distance.
B. Advanced Roles: Hazardous Materials Technician and Specialist
- Hazardous Materials Technician
- These technicians actively engage with the hazardous material, executing plans to control or stop the release.
- In-depth training in the use of various protective gear and containment equipment is required.
- Hazardous Materials Specialist
- Specialists offer technical advice on hazardous materials, often working in tandem with hazardous materials technicians.
- They have a comprehensive understanding of various hazardous substances and are adept at devising specialized containment strategies.
C. On-Scene Incident Commander: Comprehensive Responsibilities
- Role Overview
- The On-Scene Incident Commander is responsible for all aspects of the response, from strategy development to ensuring the safety of personnel.
- They require advanced training in incident management, emergency response planning, and decision-making.
- Key Responsibilities
- Commanding and coordinating emergency response efforts.
- Developing and implementing strategies to effectively manage the incident.
- Ensuring compliance with safety and environmental regulations.
- Training and Qualifications
- Extensive experience in hazardous materials handling and emergency response.
- Advanced leadership and crisis management skills are crucial.
- Typically requires a combination of specialized training and field experience.
Common Jobs and Their Corresponding HAZWOPER Training
Job Role | HAZWOPER Training Needed |
---|---|
Environmental Remediation Workers | 40-Hour HAZWOPER Training |
Hazardous Waste Site Managers | 40-Hour HAZWOPER Training, plus 8-Hour Supervisor Training |
Emergency Response Teams (Chemical Spills, Hazardous Material Incidents) | 40-Hour HAZWOPER Training or specialized emergency response training |
General Industrial Workers (in facilities that occasionally handle hazardous materials) | 24-Hour HAZWOPER Training |
Safety Officers at Hazardous Waste Sites | 40-Hour HAZWOPER Training, with possible additional requirements |
Construction Workers on Sites with Potential Hazardous Material Exposure | 24-Hour HAZWOPER Training |
Storage, Treatment, or Disposal Facility Workers | 24-Hour or 40-Hour HAZWOPER Training |
Government Inspectors for Environmental Compliance | 24-Hour HAZWOPER Training, potentially more for specialized roles |
Health and Safety Officers | 40-Hour HAZWOPER Training |
Lab Technicians Handling Hazardous Substances | 24-Hour HAZWOPER Training |
On-Scene Incident Commanders (for Hazardous Substance Incidents) | Specialized Incident Commander training |
Warehouse Personnel at Sites Storing Hazardous Materials | 24-Hour HAZWOPER Training |
Read related article: Is Hazwoper Training Hard? (How to Prepare for It)
Advanced Training for Emergency Response Situations
1. Overview of Advanced Emergency Response Training under HAZWOPER:
- HAZWOPER 29 CFR 1910.120(q): This regulation outlines the requirements for emergency response operations involving hazardous substances. Advanced training focuses on exceeding the minimum 24-hour training requirement, aiming for the full 40-hour program.
- Incident Command System (ICS) Integration: Advanced training incorporates ICS protocols, essential for managing complex hazardous incidents.
2. High-Risk Emergency Scenarios and Specialized Training Components:
- Chemical Spill and Leak Response: Training includes containment and control strategies for various hazardous substances, with an emphasis on chemical-specific properties and risks. For instance, handling a chlorine gas leak requires specific respiratory protection and evacuation procedures.
- Radiological Incident Handling: In-depth training on radiological hazard identification, including the use of Geiger counters and other radiation detection equipment. Emphasis on understanding the ALARA principle (As Low As Reasonably Achievable) for radiation exposure.
3. Advanced Personal Protective Equipment (PPE) Training:
- Level A PPE Usage: Instruction on the use of fully encapsulating chemical protective suits, SCBA (Self-Contained Breathing Apparatus), and specialized decontamination procedures.
- Respiratory Protection: Training in the selection and use of various types of respirators, including full-facepiece respirators, PAPRs (Powered Air-Purifying Respirators), and SARs (Supplied Air Respirators).
4. Hazardous Material Characterization and Assessment Techniques:
- Chemical and Physical Property Analysis: Training in using tools like NIOSH Pocket Guide to Chemical Hazards, understanding MSDS (Material Safety Data Sheets), and interpreting chemical reactivity and toxicity indicators.
- Risk Assessment Protocols: Techniques for assessing and categorizing risks associated with hazardous materials, including the use of HAZWOPER Decision Matrix.
5. Specialized Decontamination Procedures:
- Decontamination Corridor Set-up and Management: Skills in establishing and managing decontamination zones, understanding cross-contamination risks.
- Waste Management and Disposal: Training in hazardous waste packaging, labeling, and disposal in compliance with EPA (Environmental Protection Agency) regulations.
6. Advanced Emergency Medical Response and First Aid:
- Toxicology and Antidote Administration: Knowledge of common toxins and appropriate antidotes, along with advanced first aid techniques.
- Trauma Management: Skills in handling trauma cases in hazardous environments, including the use of tourniquets and emergency triage procedures.
7. Tactical Communication and Team Coordination Skills:
- Communication Protocols: Training in effective communication using radios and hand signals, especially in environments where verbal communication is hindered.
- Team Coordination: Exercises in team-based scenarios to enhance coordination and decision-making under pressure.
Advanced HAZWOPER training equips emergency responders with specialized skills and knowledge crucial for effectively managing high-risk hazardous situations. This comprehensive approach, integrating technical expertise with practical application, is essential for ensuring safety and compliance in emergency response operations involving hazardous substances.
Read related article: Who Should Take 40-Hour or 24-Hour Hazwoper Training?
HAZWOPER Training for Management and Supervisors
As specified in this rule:
Management and supervisor training. On-site management and supervisors directly responsible for, or who supervise employees engaged in, hazardous waste operations shall receive 40 hours initial training, and three days of supervised field experience (the training may be reduced to 24 hours and one day if the only area of their responsibility is employees covered by paragraphs (e)(3)(ii) and (e)(3)(iii)) and at least eight additional hours of specialized training at the time of job assignment on such topics as, but not limited to, the employer’s safety and health program and the associated employee training program, personal protective equipment program, spill containment program, and health hazard monitoring procedure and techniques.
1. Overview of Managerial HAZWOPER Training:
- OSHA 29 CFR 1910.120(e)(4): This section specifically addresses the training requirements for managers and supervisors, mandating a minimum of 8 additional hours of specialized training beyond the standard 24 or 40-hour HAZWOPER training.
- Leadership in Safety Management: Focus on developing leadership skills in safety management, including understanding of OSHA’s General Duty Clause (Section 5(a)(1) of the OSH Act), which holds supervisors responsible for providing a safe work environment.
2. Risk Assessment and Mitigation Strategies:
- Hazard Identification and Risk Analysis: Training in advanced techniques for hazard identification and risk analysis, including the use of quantitative risk assessment tools and HAZOP (Hazard and Operability Study) methodology.
- Emergency Preparedness Planning: Instruction in developing and implementing emergency response plans in accordance with OSHA’s Emergency Action Plan requirements (29 CFR 1910.38).
3. Regulatory Compliance and Enforcement:
- Understanding of OSHA 29 CFR 1910.120 and EPA Regulations: In-depth knowledge of regulatory requirements, including waste management standards under the Resource Conservation and Recovery Act (RCRA) and the Clean Air Act (CAA) compliance.
- Recordkeeping and Reporting: Training in maintaining OSHA-required records (29 CFR 1904), including injury and illness logs, and understanding the importance of accurate reporting.
4. Communication and Incident Command System (ICS):
- Effective Communication Skills: Development of skills for effective communication with both team members and regulatory agencies, focusing on clarity, accuracy, and compliance.
- ICS Familiarization: Understanding the Incident Command System structure and its application in hazardous material incidents.
5. Advanced Personal Protective Equipment (PPE) Training:
- PPE Program Management: Training in the selection, use, maintenance, and regulatory requirements of PPE (29 CFR 1910.132).
- Respiratory Protection Program: Instruction on implementing and managing a respiratory protection program in compliance with OSHA’s 29 CFR 1910.134.
6. Health and Safety Program Development:
- Safety Culture Enhancement: Strategies for fostering a strong safety culture within the organization, including behavior-based safety and continuous improvement models.
- Training Program Oversight: Skills in developing, implementing, and evaluating effective training programs for staff, tailored to specific operational hazards.
HAZWOPER training for management and supervisors emphasizes not only compliance with legal standards but also focuses on leadership in safety management, risk assessment, emergency preparedness, and effective communication. This specialized training equips leaders with the knowledge and skills necessary to oversee safe operations in hazardous waste management and emergency response scenarios, ensuring both regulatory compliance and the safety and health of workers.
Read related article: Do You Need Both HAZWOPER Training & RCRA Training?
Customizing HAZWOPER Training for Your Organization
To address the customization of HAZWOPER training for specific organizational needs, we can delve into the technical specifics:
1. Assessing Organizational Needs for HAZWOPER Training:
- Hazard Analysis and Employee Exposure Assessment: Conduct a thorough hazard analysis aligned with OSHA’s Hazard Communication Standard (29 CFR 1910.1200). This involves identifying chemical, biological, and physical hazards in the workplace and assessing employee exposure levels.
- Job Safety Analysis (JSA): Utilize JSA to determine specific job-related hazards and necessary training requirements. This involves breaking down each job task and analyzing potential risks associated with them.
- Regulatory Compliance Review: Assess the organization’s requirements under OSHA 29 CFR 1910.120, specifically sections (e) through (q), which detail training standards for various levels of employee involvement with hazardous waste operations.
2. Developing a Customized HAZWOPER Training Plan:
- Baseline Training Module Development: Based on the hazard analysis, develop baseline training modules that cover general HAZWOPER principles, including emergency response, personal protective equipment (PPE), and decontamination procedures.
- Role-Specific Training Modules: Create role-specific modules for different employee groups (e.g., field workers, emergency responders, supervisors) to address specific risks and responsibilities. For instance, emergency responders may need advanced training in incident command systems and high-risk decontamination procedures.
- Incorporating Organization-Specific Policies and Procedures: Integrate the company’s own health and safety policies, emergency response plans, and standard operating procedures (SOPs) into the training program.
- Utilization of Adult Learning Principles: Design training materials that cater to adult learning styles, incorporating interactive elements like hands-on exercises, simulations, and case studies.
3. Incorporation of Technology and Interactive Learning Tools:
- E-Learning Platforms: Leverage e-learning platforms for theoretical components of the training, ensuring flexibility and easy access for all employees.
- Simulation Training: Utilize virtual reality (VR) or augmented reality (AR) simulations for practical training in a controlled, risk-free environment.
4. Continuous Training and Skills Refreshment:
- Annual Refresher Training: Plan for OSHA-mandated 8-hour annual refresher courses to keep employees up-to-date with the latest safety practices and regulatory changes.
- Skills Assessment and Feedback Mechanisms: Implement regular skills assessments and solicit feedback to continuously adapt and improve the training program.
5. Documentation and Record Keeping:
- Training Records Management: Maintain detailed training records for each employee, including dates, course content, and assessment results, in compliance with OSHA’s recordkeeping requirements.
Customizing HAZWOPER training for an organization involves a comprehensive analysis of workplace hazards, regulatory requirements, and specific job functions. By developing tailored training modules and incorporating interactive learning tools, organizations can effectively equip their workforce with the necessary skills and knowledge to safely handle hazardous materials and respond to emergency situations, while ensuring compliance with OSHA regulations.
Read related article: Onsite Hazwoper Training: Best Method to Conduct the Course
Keeping Up with Changing Regulations and Standards
Maintaining currency with evolving OSHA regulations and industry standards, especially in the context of HAZWOPER (Hazardous Waste Operations and Emergency Response), involves a technical and strategic approach:
1. Monitoring OSHA Regulation Updates:
- Regular Review of OSHA 29 CFR 1910.120: This is the primary standard for HAZWOPER. Regular reviews, at least annually or whenever a regulatory update is announced, are crucial. It’s important to track changes in sections related to training, personal protective equipment (PPE), emergency response, and medical surveillance.
- OSHA’s e-Updates and Subscription Services: Subscribe to OSHA’s electronic newsletters and updates. Utilizing RSS feeds for real-time updates on regulatory changes can be highly effective.
2. Industry Standards and Best Practices:
- ANSI (American National Standards Institute) and NFPA (National Fire Protection Association): Keeping abreast with standards such as ANSI Z390.1 for H2S training, or NFPA 472 for hazardous materials response, is crucial for aligning with best practices.
- Engagement with Professional Bodies: Joining industry associations like the American Society of Safety Professionals (ASSP) or the AIHA (American Industrial Hygiene Association) for access to seminars, workshops, and publications on the latest industry standards.
3. Continuous Learning and Training Refreshers:
- Annual 8-Hour Refresher Training: Mandated under OSHA 29 CFR 1910.120(e)(8), this refresher training is essential for employees to stay current with any changes in procedures, technologies, and regulations.
- Integration of New Knowledge into Existing SOPs: Regularly updating Standard Operating Procedures (SOPs) to incorporate new regulatory information and best practices.
4. Utilization of Digital Tools and Resources:
- Learning Management Systems (LMS): Employing an LMS to disseminate updates and new training materials efficiently across the organization.
- Online Forums and Webinars: Participating in webinars and online forums can provide insights into how other organizations are adapting to regulatory changes.
5. Internal Compliance Audits and Reviews:
- Regular Safety Audits: Conducting internal audits to ensure compliance with current OSHA standards and industry best practices.
- Hazard Communication Program Updates: Keeping the Hazard Communication Program (29 CFR 1910.1200) up-to-date with the latest safety data sheets (SDS) and labeling requirements.
6. Encouraging a Culture of Safety and Compliance:
- Employee Involvement in Continuous Learning: Encouraging employees to stay informed about changes in safety standards and participate in ongoing education initiatives.
- Leadership and Management Training: Ensuring that leadership and management are trained to understand the importance of compliance and are equipped to enforce and advocate for safety standards.
Staying updated with OSHA regulations and industry standards is a dynamic process that requires a proactive approach, continuous learning, and regular training refreshers. Integrating new knowledge into organizational practices, leveraging digital tools for efficient information dissemination, and fostering a culture of safety and compliance are key to adapting to regulatory changes in the field of hazardous waste operations and emergency response.
Evaluating and Selecting a HAZWOPER Training Provider
First and foremost, let’s clear that OSHA does not provide training and endorse any training provider, as stated:
Can you recommend an on-line HAZWOPER (8-, 24-, or 40-hour) course?
OSHA does not recommend, approve, certify, or endorse individual trainers or training programs. It is OSHA’s policy that use of computer-based training by itself would not be sufficient to meet the intent of the standard’s various training requirements. There are two primary considerations for you to explore before deciding whether to take an on-line HAZWOPER course.
Citation: OSHA; https://www.osha.gov/emergency-preparedness/hazardous-waste-operations/faq
- For HAZWOPER training, it is essential that the trainees have hands-on experience and exercises that provide an opportunity to become familiar with equipment and safe practices in a non-hazardous setting. The purpose of hands-on training (e.g., donning and doffing of protective equipment, using air monitoring equipment) is two-fold: first, to ensure that workers have an opportunity to learn by practical experience and second, to assess whether workers have mastered the necessary skills. Employers need to know how an on-line course provides this hands-on training.
- Also, in an effective training program, it is critical that trainees have the opportunity to ask questions where material is unfamiliar to them. Providing access to a telephone hotline or an e-mail contact at the time of the training so that trainees will have direct access to a qualified trainer at the time their questions are raised is one way a computer-based training program may accomplish this requirement.
Evaluating and selecting a HAZWOPER training provider involves a detailed process to ensure that the training meets regulatory standards and organizational needs. Here are the key criteria and the importance of accreditation and industry recognition:
1. Accreditation and Certification:
- OSHA Authorization: Verify that the training provider is authorized by OSHA to deliver HAZWOPER training. This ensures compliance with OSHA 29 CFR 1910.120 standards.
- Industry Recognitions: Look for providers recognized by relevant industry bodies, such as the National Environmental Safety and Health Training Association (NESHTA) or the Board of Certified Safety Professionals (BCSP).
2. Course Content and Relevance:
- Curriculum Compliance: Ensure the curriculum aligns with OSHA’s HAZWOPER standards. The training should cover all essential topics like personal protective equipment (PPE), emergency response, exposure monitoring, and decontamination procedures.
- Customization Capabilities: Assess if the provider offers customized training options that can be tailored to your specific industry and organizational needs.
3. Instructor Expertise and Experience:
- Qualified Instructors: Instructors should have relevant industry experience and professional qualifications in environmental health and safety.
- Teaching Methodology: Evaluate the instructors’ ability to deliver content effectively, engagingly, and interactively, which is crucial for adult learning.
4. Training Delivery Methods:
- Flexibility in Training Modes: Consider providers that offer various training modes, such as in-person, online, and hybrid models, to accommodate different learning preferences and logistical requirements.
- Hands-On Training and Simulations: Availability of practical, hands-on training sessions and simulations is crucial for effective learning, especially for emergency response training.
5. Assessment and Certification Process:
- Rigorous Assessment: Check that the provider has a rigorous assessment methodology to ensure trainees understand and can apply the training content.
- Certification: Ensure the training concludes with a certification that is recognized and respected in the industry.
6. Post-Training Support and Resources:
- Continued Learning Opportunities: Availability of refresher courses, updated materials, and ongoing support post-training.
- Access to Resources: Provision of additional learning resources, such as manuals, online content, and industry updates.
7. Cost-Effectiveness and ROI:
- Transparent Pricing: Look for providers with transparent pricing structures with no hidden costs.
- Return on Investment (ROI): Consider the long-term benefits of the training in terms of improved safety, compliance, and reduced risk of incidents.
8. Reviews and Testimonials:
- Client Feedback: Research and read reviews, testimonials, and case studies from previous clients to gauge the effectiveness and reputation of the provider.
Selecting the right HAZWOPER training provider is a critical decision that impacts an organization’s compliance, safety culture, and operational efficiency. Prioritizing accreditation, the relevance and quality of course content, instructor expertise, and the overall value offered by the training provider will ensure that the organization’s investment in HAZWOPER training is sound and effective.
Conclusion
Selecting the right HAZWOPER training doesn’t have to be complicated. It all depends on your job and how often you deal with hazardous materials. If your work involves regular handling of dangerous substances, like in waste clean-up or emergency responses, the 40-hour training is for you.
For those who work around these hazards less frequently, the 24-hour course might be enough. And remember, if you already have HAZWOPER training, don’t forget the 8-hour refresher course every year to keep your skills sharp and stay safe on the job. For supervisors, an additional 8-hour course is needed to learn how to keep your team safe. The main goal is to ensure everyone goes home safely at the end of the day, and the right training can make all the difference.