Custom HAZWOPER Training for Companies: The Right Approach
November 13, 2023 | by onlineoshasafetytraining.com
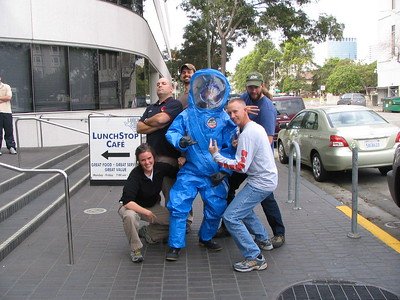
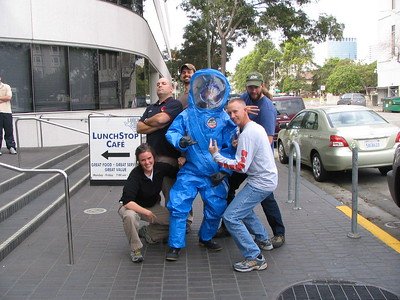
Absolutely! Customizing HAZWOPER training for your company is not only possible but highly beneficial. Tailoring the training to meet the specific needs of your workforce and the unique hazards they face can significantly enhance the effectiveness of the training program. Customized training can address particular operational procedures, emergency response scenarios, and safety protocols relevant to your company’s environment.
This approach ensures that your employees are not only compliant with regulatory standards but also well-prepared and confident in handling the specific hazardous situations they might encounter in their line of work. By investing in this HAZWOPER training, you’re investing in a safer and more proficient workforce.
If you want to have a tailored training curriculum, here is a brief guide… Read on…
Understanding HAZWOPER Training
Sure, let’s break down the concept of the training in a straightforward way:
- What is HAZWOPER?
- HAZWOPER stands for Hazardous Waste Operations and Emergency Response.
- It’s a type of training for people who work with hazardous substances, especially during cleanup, emergency response, or storage operations.
- OSHA’s Rules and Standards
- OSHA, the Occupational Safety and Health Administration, sets the rules for HAZWOPER.
- They require certain workers to be trained so they can safely handle hazardous waste and respond to emergencies.
- OSHA’s standards are detailed in a regulation called 29 CFR 1910.120.
- Standard Training Modules
- The training usually includes 40 hours of coursework for workers at hazardous sites and 24 hours for less hazardous operations.
- There’s an 8-hour refresher course required yearly.
- Key topics include recognizing hazards, wearing protective gear, emergency procedures, and decontamination methods.
This training is essential to keep workers safe and to comply with legal standards when dealing with dangerous materials.
Read related article: HAZWOPER 40-hour Course Schedule (The Typical 5-Day Plan)
Why is There a Need for Customization in HAZWOPER Training
Customizing the training is essential because standard training might not fully cover the unique risks and operational practices of different companies. Each company faces its own specific set of hazards based on its industry, location, and operations. By tailoring the training to these specific risks, employees receive more relevant and practical knowledge, enhancing their ability to respond effectively in real-world scenarios.
Additionally, companies often have unique internal procedures and emergency response plans. tailored training allows these company-specific protocols to be integrated into the training program, making it more directly applicable to the employees’ daily work environment.
Regulatory compliance is another critical factor. Different industries and areas may have additional legal requirements beyond the general HAZWOPER standards. Tailored training ensures that these specific regulations are addressed, helping companies to avoid legal issues and maintain a safe work environment.
- Limitations of Standard ‘One-Size-Fits-All’ Training
- Standard HAZWOPER training typically covers general procedures and practices for handling hazardous waste and emergency situations.
- This generic approach may not address the specific risks or procedures associated with different industries or companies.
- For example, a chemical manufacturing plant and a petroleum refinery, although both handling hazardous materials, face very different kinds of risks and emergencies.
- Industry-Specific Hazards and Emergencies
- Different industries have unique hazards. For instance, a pharmaceutical company might deal with biohazards, while a battery manufacturer faces risks with lead and acid.
- Emergency scenarios also vary. A gas leak emergency in a natural gas plant requires different protocols than a chemical spill in a laboratory.
- Standard training might not cover these specific scenarios in detail, which can leave employees underprepared.
- Advantages of Customized Training
- Targeted Risk Management: Custom training can be developed to address specific hazards unique to a company’s operations. This targeted approach ensures that workers are well-versed in handling the specific substances and situations they encounter.
- Enhanced Emergency Preparedness: Tailoring the training allows for inclusion of company-specific emergency response plans and procedures, ensuring that employees are prepared for the exact types of emergencies they might face.
- Increased Compliance Relevance: Tailored training can be aligned more closely with the company’s compliance requirements, addressing any specific local, state, or federal regulations applicable to their operations.
- Employee Engagement and Retention: Training that is directly relevant to an employee’s day-to-day tasks is more engaging and easier to retain, leading to a more competent and confident workforce.
Modifying HAZWOPER training is essential for addressing the unique hazards and emergency scenarios specific to a company’s industry and operations. This tailored approach not only enhances safety and preparedness but also ensures more relevant and effective training for employees.
Read the related article: Is Hazwoper Training Hard? (How to Prepare for It)
Understanding the Scope of Custom HAZWOPER Training
Custom Training Explained
- Definition and Scope
- Tailored HAZWOPER training is tailored to address the unique hazardous waste challenges faced by a specific company.
- It involves a detailed risk assessment, considering variables like toxic substance concentrations (measured in ppm – parts per million), site-specific hazardous waste types, and unique operational environments (e.g., confined space entry requirements).
- Technical Components
- Custom training may include specialized modules on handling specific hazardous substances, like polychlorinated biphenyls (PCBs) at concentrations above 50 ppm, or dealing with specific waste forms such as sludges, solids, or gases.
- The training might also focus on advanced personal protective equipment (PPE) usage, detailing specific suits (like Level A, B, C, or D) depending on the chemical exposure risk, which can range from <10 ppm (requiring Level D protection) to >1000 ppm (necessitating Level A protection).
Differences Between Standard and Customized Training
- Curriculum Focus
- Standard HAZWOPER training typically covers broad topics in a generalized format, such as basic chemical hazard recognition, standard PPE usage, and generic emergency response procedures.
- Custom training, conversely, delves into specific chemical hazards relevant to the company, such as chlorine gas handling in a water treatment facility, where exposure levels might routinely be in the 1-3 ppm range, demanding specific respiratory protection.
- Practical Applications and Scenarios
- Standard training often uses generalized scenarios, like a hypothetical spill of a common chemical.
- Custom training employs real-world scenarios from the company’s past incidents, like a specific spill of hydrochloric acid (HCl) at 500 ppm, requiring detailed decontamination procedures using sodium bicarbonate (NaHCO3) solutions.
- Regulatory Compliance and Site-Specific Standards
- Standard training adheres to OSHA’s baseline HAZWOPER requirements, such as the 24-hour or 40-hour training for general site workers (29 CFR 1910.120).
- Custom training integrates company-specific regulations and standards, like incorporating EPA’s Resource Conservation and Recovery Act (RCRA) requirements for waste handling in a facility managing hazardous waste over 100 kg/month.
- Assessment and Certification Criteria
- Standard training follows a uniform assessment method, often including a test on general knowledge.
- Custom training includes assessments tailored to the specific operational and emergency protocols of the company, often incorporating practical demonstrations of skills, like using a particular type of respirator or neutralizing a specific chemical spill.
Custom training is more technically detailed, focusing on specific hazards, equipment, and scenarios relevant to a particular company, compared to the broader approach of standard HAZWOPER training. This specificity includes tailored curriculum components, practical applications, compliance aspects, and assessment criteria.
Read related article: Easy Way to Check HAZWOPER Certification
Identifying Company-Specific Hazardous Material Challenges
When identifying company-specific hazardous material challenges, a technical approach that uses precise measurements, numbers, and industry-specific terms is crucial. This section will break down the process into assessing unique hazardous scenarios and reviewing industry-specific case studies.
Assessing Unique Hazardous Material Scenarios
- Industry-Specific Hazard Identification
- Chemical Manufacturing: Focus on the handling and storage of reactive chemicals like ethylene oxide, with concentration limits set at 800 ppm for explosion risk.
- Pharmaceutical Industry: Emphasis on cytotoxic drug handling, where permissible exposure limits (PELs) might be as low as 0.1 µg/m³ for certain compounds.
- Risk Assessment Metrics
- Utilizing Threshold Limit Values (TLVs) and PELs to assess exposure risks. For instance, in a petroleum refinery, benzene exposure must be monitored closely, with OSHA setting a PEL of 1 ppm averaged over an 8-hour workday.
- Application of Industrial Hygiene principles to evaluate the risk of chemical exposure, considering factors like vapor pressure, which can indicate the likelihood of inhalation hazards.
Case Studies of Industry-Specific Hazardous Waste Challenges
- Chemical Plant Explosion Analysis
- Scenario: A chemical plant where a mixture of volatile organic compounds (VOCs) exceeded safe storage temperatures, leading to an explosion.
- Technical Analysis: Examination of storage conditions, VOC concentrations (measured in parts per billion, ppb), and the auto-ignition temperatures of the chemicals involved.
- Pharmaceutical Industry Contamination Incident
- Scenario: An incident involving accidental release of active pharmaceutical ingredients (APIs) into the environment, leading to contamination.
- Analysis: Measurement of APIs in soil and water samples, with concentrations quantified in nanograms per liter (ng/L), and assessment of containment breach protocols.
- Mining Industry Heavy Metal Leaching
- Scenario: Heavy metal leaching from mine tailings into groundwater.
- Analysis: Quantification of heavy metals like lead (Pb) and arsenic (As) in groundwater, using parts per trillion (ppt) measurements, and evaluation of tailings storage and containment methods.
- Oil Refinery Hazardous Waste Management
- Scenario: Spill of crude oil in a refinery, leading to soil and water contamination.
- Analysis: Measuring hydrocarbon levels in contaminated areas, using Total Petroleum Hydrocarbons (TPH) analysis, and reviewing spill response and containment strategies.
Each case study and scenario assessment in different industries revolves around specific technical measurements (like ppm, ppb, µg/m³) and focuses on unique hazardous materials and waste challenges, providing an in-depth understanding of the varied risks and appropriate mitigation strategies.
Read related article: How to Complete the HAZWOPER Field Training?
Here is a Guide on How to Design a Customized Training Program
Designing a HAZWOPER training program that suits your company involves a detailed and structured approach to ensure it meets the specific needs of your company. Here’s a more detailed, step-by-step guide with technical terms:
- Conduct a Hazard Analysis
- Begin by performing a comprehensive hazard analysis.
- Identify the types of hazardous materials and conditions your employees are likely to encounter, such as toxic chemicals, flammable substances, or biohazards.
- Assess the potential for exposure and the specific risks associated with these materials.
- Determine Training Requirements
- Based on the hazard analysis, determine the OSHA-required training levels.
- Consider the roles of employees: Will they require 24-hour or 40-hour HAZWOPER training? Do supervisors need additional training?
- Engage Subject Matter Experts
- Involve industry-specific experts in the development of training content.
- These experts can provide insights into best practices for handling specific hazardous materials and emergency response procedures.
- Develop Tailored Content
- Create training modules that address the identified hazards and scenarios.
- Integrate industry-specific risk assessments, material safety data sheet (MSDS) interpretation, and site-specific emergency response protocols.
- Incorporate Practical Exercises
- Include hands-on exercises that simulate real-life scenarios, like spill response drills or decontamination procedures.
- Ensure these exercises are relevant to the specific types of hazards present in your workplace.
- Integrate Company Policies and Procedures
- Tailor the training to include your company’s internal safety policies, standard operating procedures (SOPs), and emergency action plans.
- Ensure that the training aligns with both OSHA standards and your company’s internal compliance requirements.
- Review and Revise Training Materials
- Regularly review and update the training program to reflect changes in workplace hazards, new regulatory requirements, or updates in safety technology and best practices.
- Pilot Test the Program
- Before full implementation, conduct a pilot test of the training program with a small group of employees.
- Gather feedback to make any necessary adjustments.
- Implement and Evaluate
- Roll out the training to all relevant employees.
- Continuously evaluate the effectiveness of the training through assessments, feedback, and workplace safety performance metrics.
Designing a tailored training curriculum for HAZWOPER (Hazardous Waste Operations and Emergency Response) requires a technical approach that incorporates specific measurements, numbers, and detailed procedures. Here’s how such a curriculum can be developed:
Steps to Develop a Customized Training Program
- Hazard Analysis and Curriculum Customization
- Conduct a detailed hazard analysis, identifying specific chemicals and their concentrations. For instance, identifying solvents like toluene present at 300 ppm in a manufacturing setting.
- Develop modules based on identified hazards, such as a module specifically on toluene exposure control and spill response procedures.
- Dose-Response Relationship and Exposure Limits
- Include training on understanding dose-response relationships and exposure limits, such as explaining the difference between Time-Weighted Average (TWA), Short-Term Exposure Limit (STEL), and Ceiling limits.
- Use real data from the workplace, like historical TWA exposure levels for various chemicals, to make the training more relevant.
- Standard Operating Procedures (SOPs) Alignment
- Align training with company-specific SOPs, ensuring that all procedures reflect the latest operational practices, like specific decontamination steps for a chemical spill in the facility.
Read related article: What Does Hazwoper Training Cover?
Incorporating Company-Specific Safety Protocols and Emergency Procedures
- Custom Emergency Response Plans
- Tailor emergency response plans to the company’s specific needs, such as procedures for handling a chemical leak of hydrochloric acid (HCl) with a concentration of 500 ppm, which might include specific neutralization techniques using sodium bicarbonate (NaHCO3).
- Include training on the use of specific safety equipment unique to the site, such as respirators with cartridges rated for specific chemical exposures.
- Risk Assessment and Control Strategies
- Train employees on conducting risk assessments using technical tools like Job Safety Analysis (JSA) and Hazard and Operability Study (HAZOP).
- Incorporate control strategies like engineering controls (e.g., ventilation systems capable of maintaining airborne contaminants below 50 ppm).
Integrating Advanced Technology and Simulations for Realistic Training Scenarios
- Simulation-Based Training
- Use virtual reality (VR) simulations to create immersive scenarios, such as a VR module that simulates a spill of a specific chemical, like benzene, and teaches appropriate response actions under various concentration scenarios (e.g., 10 ppm, 50 ppm, 100 ppm).
- Implement augmented reality (AR) for equipment training, allowing trainees to interact with virtual models of complex machinery or hazardous material containers.
- Quantitative Feedback Mechanisms
- Incorporate sensors and tracking systems in simulations to provide quantitative feedback on trainees’ performance, like measuring response time in handling a simulated chemical spill.
- Use data analytics to assess the effectiveness of training, analyzing metrics like incident response times and decision-making accuracy in simulated emergencies.
Read related article: Which HAZWOPER Training Do You Need? (Different Levels)
If You Want a Tailored Curriculum, Talk to the Training Provider
If you’re seeking a tailored curriculum for HAZWOPER training, it’s crucial to have a detailed discussion with the training provider. Here are some key points to consider during this conversation:
- Specify Your Company’s Needs: Clearly communicate the specific risks, operational practices, and types of hazardous materials your employees encounter. This helps the training provider understand the unique aspects of your company.
- Discuss Industry-Specific Scenarios: Share any unique emergency scenarios or situations that are relevant to your industry. This enables the training provider to develop scenarios and drills that are pertinent to your employees.
- Inquire About Customization Options: Ask the training provider about their ability to tailor the curriculum. This includes how they can integrate your company’s internal safety protocols and emergency procedures into the training.
- Review Compliance Requirements: Make sure the training provider is aware of any specific regulatory requirements that apply to your industry or location. The training should cover these to ensure your company remains compliant.
- Evaluate Training Methodologies: Discuss the methods of training delivery, like in-person, online, or blended learning options. Also, consider if they offer interactive elements like hands-on training or simulations, which can enhance learning.
- Request Examples of Specific Training: Ask for case studies or examples where the provider has successfully tailored training for other companies. This can give you an idea of their expertise and capability in modifying the training.
- Clarify Costs and Logistics: Understand the cost implications of customized training and discuss the logistics, such as training location, duration, and schedule.
By having a thorough discussion with the training provider and addressing these points, you can ensure that the HAZWOPER training your employees receive is well-suited to your company’s specific needs and circumstances.
Read related article: Is In-Person Hazwoper Training Right for You? (Its Benefits)
Customized Training Program Can Be More Expensive
That’s true, a customized training program, including those for HAZWOPER, can often be more expensive than standard, off-the-shelf training courses. Here’s why:
- Tailoring Content: Developing a program that specifically addresses your company’s unique hazards, procedures, and compliance requirements involves additional work in terms of research, development, and adaptation of training materials.
- Expert Involvement: This training may require the input of industry-specific experts or specialists who understand the unique risks associated with your company’s operations. Hiring these experts can add to the cost.
- Training Delivery: If this training includes unique delivery methods, like hands-on simulations or the use of specialized equipment, this can increase the cost compared to standard classroom-based or online training.
- Revisions and Updates: Tailoring a program often means that it may need to be updated more frequently to reflect changes in your company’s operations, technology, or industry regulations, leading to additional costs over time.
However, it’s important to weigh these costs against the potential benefits of a tailored training program, such as improved safety, better compliance, and more effective learning outcomes for employees. In many cases, the investment in this training can lead to long-term savings by reducing accidents, improving efficiency, and ensuring regulatory compliance.
Read related article: Where Can You Get Free HAZWOPER Training?
Delivery Methods for Custom HAZWOPER Training
For custom training, there are several delivery methods, each with its own advantages. Understanding these methods can help in choosing the most effective approach for your company:
- Traditional In-Person Training
- This method involves face-to-face instruction, typically in a classroom setting.
- It’s beneficial for direct interaction between trainers and trainees, allowing for immediate feedback and clarification.
- Hands-on components, like using actual equipment or practicing emergency response drills, are easier to incorporate.
- Online Training Platforms
- Online training offers flexibility, as employees can complete modules at their own pace and schedule.
- It’s cost-effective, especially for companies with multiple locations, as it reduces travel and accommodation expenses.
- However, it may lack the hands-on experience and direct interaction found in in-person training.
- Interactive and Hands-On Training Methods
- Interactive training can include workshops, simulations, and practical exercises.
- These methods are crucial for HAZWOPER training as they provide real-life experience in handling hazardous materials and responding to emergencies.
- They enhance retention and ensure employees are better prepared for actual workplace scenarios.
- Utilizing Virtual Reality (VR) or Augmented Reality (AR)
- VR and AR are emerging as powerful tools for immersive training experiences.
- They simulate hazardous scenarios in a safe, controlled environment, allowing employees to practice their response to emergencies without real-world risks.
- This technology can make training more engaging and realistic, providing a deep understanding of complex situations.
Each of these methods has its strengths, and often a blended approach is most effective. For instance, combining online theoretical learning with in-person practical exercises can provide both flexibility and hands-on experience. VR and AR can further enhance this experience, adding a level of realism and engagement that can significantly improve training outcomes.
If You Are Hiring or Designating a Trainer for Onsite Training, Understand This
1910.120(q)(7) – Trainers: Trainers who teach any of the training required must have satisfactorily completed a training course for teaching the subjects they teach. Otherwise trainers must have the training and/or academic credentials and instructional experience to demonstrate that they are competent to teach and that they have good command of the subject matter they teach.
Citataion: OSHA Standards; https://www.osha.gov/emergency-preparedness/hazardous-waste-operations/standards
Instructors tasked with conducting specific training courses must meet stringent qualification criteria. They should have either completed an accredited training program directly related to the subjects they intend to teach or, alternatively, they must demonstrate a robust combination of relevant educational credentials and practical training. Additionally, these trainers should have substantial experience in instruction, underscoring their ability to effectively teach and convey deep, comprehensive knowledge of the subject matter. This ensures that they are not only proficient in their field but also skilled in the art of teaching, thereby enhancing the overall quality and effectiveness of the training they provide.
Prepare for the Challenges and Here are the Possible Solutions
Preparing for challenges in custom HAZWOPER training involves understanding the potential issues and finding ways to solve them. One common challenge is making sure the training is relevant to the specific needs of your company. To overcome this, work closely with training providers to tailor the content to your company’s unique risks and procedures.
Another challenge is keeping employees engaged, especially if the training is long or complex. Using interactive methods like hands-on exercises or simulations can help keep learners interested and make the training more effective.
Also, it’s important to regularly update the training program. The needs of your company, as well as regulations and industry standards, can change. Regular reviews and updates ensure that the training stays current and effective.
Lastly, balancing cost and quality is a challenge. This training can be more expensive than standard programs. To manage this, focus on the most critical areas for Specific and use a mix of online and in-person training to control costs while still providing effective learning experiences.
Overall, preparing for these challenges with thoughtful strategies can lead to a successful and impactful HAZWOPER training program that meets your company’s requirements.
Regulatory Compliance and Custom Training
Navigating complex regulations and ensuring that training meets legal requirements involve a detailed understanding of technical standards, measurements, and legal criteria. Collaborating with regulatory bodies to tailor training programs also requires a nuanced approach. Here’s an in-depth look at these aspects:
Navigating Complex HAZWOPER Regulations
- Understanding OSHA’s HAZWOPER Standards
- HAZWOPER regulations, under OSHA 29 CFR 1910.120, mandate specific training requirements based on roles and exposure risks. For example, workers with 24-hour training are limited to specific operations with hazardous substances not exceeding PELs (Permissible Exposure Limits) like benzene at 1 ppm over an 8-hour TWA (Time-Weighted Average).
- Tailored training programs must incorporate these baseline requirements, tailoring them to specific workplace scenarios, like handling unique chemical hazards where exposure levels might frequently exceed OSHA’s action levels (e.g., 0.5 ppm for benzene).
- Adherence to EPA and DOT Regulations
- Incorporating EPA regulations on hazardous waste management, such as RCRA (Resource Conservation and Recovery Act) requirements for facilities generating more than 100 kg of hazardous waste per month.
- Understanding DOT (Department of Transportation) regulations for the transport of hazardous materials, including specific packaging and labeling requirements based on the Hazardous Materials Table (49 CFR 172.101).
Ensuring Custom Training Meets Legal Requirements
- Alignment with National Standards
- Tailored training programs must align with national consensus standards like NFPA 472, which sets competencies for hazardous materials responders. For instance, detailing procedures for PPE selection based on specific chemical properties, such as flash points and corrosivity.
- Incorporate ANSI (American National Standards Institute) standards where applicable, for example, ANSI Z87.1 for eye and face protection in chemical exposure scenarios.
- Record Keeping and Documentation
- Maintain detailed records of all training activities, including specific modules covered, hours of instruction, and assessment results, in compliance with OSHA’s recordkeeping requirements.
- Implement systems to track and document employee exposure levels to hazardous substances, ensuring compliance with OSHA’s 29 CFR 1910.1020 for employee medical and exposure records.
Collaboration with Regulatory Bodies for Tailored Training Programs
- Engaging with OSHA Consultation Programs
- Utilize OSHA’s On-site Consultation Program to get expert advice on personalized training programs to meet specific workplace hazards, ensuring that both the spirit and letter of the regulations are followed.
- Regularly update training content based on feedback and guidance from OSHA consultants, particularly when new regulations or changes to existing standards occur.
- Partnerships for Continuous Improvement
- Establish partnerships with industry associations or regulatory bodies for continuous improvement of the training program. This could involve incorporating cutting-edge research on hazardous materials handling or emerging best practices in emergency response.
- Engage in workshops and seminars conducted by agencies like the EPA or industry-specific safety organizations to stay abreast of new developments and integrate them into the custom training program.
Ensuring regulatory compliance in custom HAZWOPER training involves a deep understanding of various legal requirements, from OSHA standards to EPA and DOT regulations. It requires aligning training programs with national standards, maintaining rigorous record-keeping, and actively collaborating with regulatory bodies to ensure the training remains relevant, comprehensive, and legally compliant.
Continuous Improvement and Feedback Mechanisms
Implementing continuous improvement and feedback mechanisms in HAZWOPER (Hazardous Waste Operations and Emergency Response) training programs is essential to ensure they remain effective, up-to-date, and aligned with evolving industry practices. Here’s a detailed approach:
Establishing Feedback Loops for Continuous Improvement
- Post-Training Evaluations
- Implement detailed post-training evaluations using quantitative and qualitative metrics. For example, use a Likert scale (ranging from 1 to 5) to gauge trainees’ confidence in handling specific hazardous scenarios post-training.
- Conduct skill assessments to quantitatively measure improvements in handling emergency situations, like timed drills for donning PPE or executing a decontamination procedure.
- Regular Feedback Sessions
- Organize regular feedback sessions with trainees, trainers, and safety managers to discuss the efficacy of the training modules. Focus on specific areas like the clarity of instructions for using specialized equipment or effectiveness of hands-on training components.
- Use tools like anonymous surveys or suggestion boxes to encourage honest feedback.
- Real-time Monitoring and Analytics
- Employ monitoring tools during training sessions to gather real-time data. For instance, use sensors in training equipment to track the accuracy and speed of responses in simulated emergency scenarios.
- Analyze this data to identify trends or areas needing improvement, such as consistently missed steps in emergency protocols.
Methods for Updating Training Based on Evolving Industry Practices and Incident Learnings
- Incorporation of Incident Reports and Case Studies
- Regularly update the training curriculum with recent incident reports and case studies relevant to the industry. For example, if a new type of chemical spill incident occurs in the industry, incorporate it into the training as a case study.
- Analyze these incidents to understand what went wrong and how similar situations can be handled more effectively, updating training modules accordingly.
- Staying Abreast with Industry Developments
- Continuously monitor industry developments, such as new hazardous materials being used, changes in regulatory standards, or advances in safety equipment and procedures.
- Attend industry conferences, workshops, and webinars, and subscribe to relevant journals and publications to stay updated.
- Regular Training Program Reviews and Updates
- Schedule periodic reviews of the training program, involving experts in the field, to ensure that the content remains current and comprehensive.
- Implement a structured process for regularly updating the training material, incorporating new technologies, best practices, and regulatory changes.
- Collaboration with External Experts
- Collaborate with external safety consultants, regulatory bodies, and industry experts to gain insights into the latest trends and best practices in hazardous material handling and emergency response.
- Consider joint training exercises with external agencies or neighboring companies to bring in new perspectives and learning opportunities.
By establishing robust feedback mechanisms and keeping the training program aligned with evolving industry practices and incident learnings, companies can ensure their HAZWOPER training remains effective, relevant, and capable of preparing employees for real-world hazardous situations.
Measuring the Impact of Customized Training
Measuring the impact of this training involves using specific criteria and methods that are technical and quantitative, ensuring an accurate assessment of training effectiveness. Additionally, understanding the long-term benefits of such training is crucial for employee safety and company compliance.
Criteria and Methods for Assessing the Effectiveness of Custom HAZWOPER Training
- Quantitative Performance Metrics
- Pre- and Post-Training Assessments: Conduct detailed knowledge and skill tests before and after training sessions. Measure improvements in scores, aiming for a quantifiable increase (e.g., 20% improvement in test scores).
- Incident Response Time: Track the response time to simulated emergencies pre- and post-training. A reduction in response time (e.g., from 10 minutes to 7 minutes) indicates improved efficiency.
- Qualitative Feedback Analysis
- Employee Confidence Levels: Use surveys or interviews to gauge employee confidence in handling hazardous materials and emergency situations. Employ a 5-point scale to quantify confidence levels and track changes over time.
- Trainer and Supervisor Evaluations: Incorporate evaluations from trainers and supervisors, focusing on specific competencies and practical skills demonstrated during training exercises.
- Compliance and Safety Metrics
- OSHA Compliance Rate: Monitor the rate of compliance with OSHA regulations pre- and post-training, aiming for a higher percentage of compliance.
- Accident and Incident Rates: Track the frequency of accidents or near-misses involving hazardous materials. A decrease in these incidents post-training indicates effectiveness.
Long-Term Benefits of Customized Training for Employee Safety and Company Compliance
- Enhanced Employee Safety
- Reduced Exposure to Hazards: Custom training can lead to more effective handling of hazardous materials, thus reducing exposure levels. For example, fewer instances of exposure above PELs (Permissible Exposure Limits), such as benzene exposure not exceeding 1 ppm over an 8-hour TWA.
- Improved Emergency Preparedness: Employees are better prepared to handle emergency situations, reducing the potential severity of incidents. For instance, more efficient containment of chemical spills, reducing environmental and health impacts.
- Increased Company Compliance
- Adherence to Regulatory Standards: Custom training ensures that employees are well-versed in industry-specific regulations, leading to higher compliance rates with standards like OSHA 29 CFR 1910.120 and EPA guidelines.
- Documentation and Record-Keeping: Enhanced training results in better documentation practices, meeting regulatory requirements for training records and incident reporting.
- Long-Term Cost Savings
- Reduction in Safety-Related Costs: Effective training can lead to a decrease in costs associated with accidents, such as reduced workers’ compensation claims and lower insurance premiums.
- Efficiency in Hazardous Materials Management: Improved handling and disposal of hazardous materials can lead to cost savings, such as reduced waste disposal fees or penalties for non-compliance.
The impact of this HAZWOPER training can be measured through a combination of quantitative performance metrics, qualitative feedback, compliance rates, and safety metrics. The long-term benefits include enhanced employee safety, increased compliance with regulatory standards, and potential cost savings for the company.
Conclusion
The implementation of custom HAZWOPER training for companies marks a significant stride towards heightened workplace safety, regulatory adherence, and operational efficiency in handling hazardous materials. Unlike standard, one-size-fits-all training programs, tailored training offers a tailored approach that addresses the specific needs and risks associated with different industries and individual companies. This tailored training not only ensures compliance with OSHA and other regulatory bodies but also embeds a deeper understanding and practical skillset among employees regarding the safe handling of hazardous substances and emergency response procedures.
The effectiveness of tailored training programs is measurable and manifests in various forms – from improved employee performance metrics and enhanced safety protocols to reduced incident rates and adherence to legal standards. The incorporation of real-world scenarios, specific to the company’s operational environment, significantly increases the relevance and effectiveness of the training. Moreover, the continual updating of these programs in line with evolving industry practices and technological advancements further solidifies their efficacy.
Investing in custom HAZWOPER training is not merely a regulatory obligation but a strategic decision that yields long-term benefits. These benefits extend beyond compliance, fostering a culture of safety and awareness within the organization. It leads to a workforce that is not only well-prepared to handle hazardous situations but also contributes to a safer, more efficient, and environmentally responsible workplace.
In conclusion, custom HAZWOPER training stands as an indispensable component in the realm of industrial safety. It is a proactive approach that equips companies to effectively manage the inherent risks associated with hazardous materials, ensuring the well-being of their employees and the surrounding environment, while simultaneously maintaining operational excellence.
RELATED POSTS
View all