All blog posts
Explore the world of design and learn how to create visually stunning artwork.
Are Forklift Certifications Transferable? (What To Do If It Isn’t)
April 6, 2024 | by onlineoshasafetytraining.com
How To Find Forklift Training With Job Placement?
April 6, 2024 | by onlineoshasafetytraining.com
Can You Take Forklift Training Even With No Experience?
April 6, 2024 | by onlineoshasafetytraining.com
How To Pass Forklift Training 2024? (Written & Practical Tests)
April 5, 2024 | by onlineoshasafetytraining.com
Do You Have To Be Certified To Train Forklift Operator?
April 5, 2024 | by onlineoshasafetytraining.com
Who Can Do Forklift Training (5 Pros Who Can Do This)
April 3, 2024 | by onlineoshasafetytraining.com
How To Get Free Online Forklift Training (Easy Ways to Do It)
March 23, 2024 | by onlineoshasafetytraining.com
Online Forklift Certification in BC
March 23, 2024 | by onlineoshasafetytraining.com
How Long Does It Take To Get Forklift Certified Online?
March 23, 2024 | by onlineoshasafetytraining.com
Can You Drive A Forklift Without Certification? (Is It Required?)
March 23, 2024 | by onlineoshasafetytraining.com
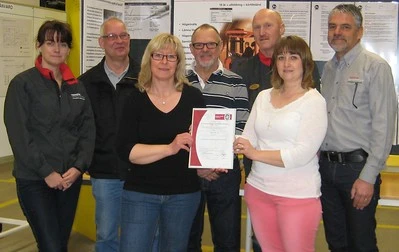
So, if you’ve got a forklift certification from your present company and you’re wondering if it is transferrable and you can just take it with you to a new job like you do with your lunchbox, the straight-up answer is nope, you can’t.
But don’t sweat it! Just because the piece of paper that says you’re certified to drive a forklift at one place doesn’t automatically get you in the driver’s seat at another, your skills and experience you’ve racked up are still super valuable.
Think of it like this: when you play video games and get really good at one game, those gaming skills help you catch on quicker in other games, right? It’s kind of the same deal. You’ve already got the know-how and the moves; you just might need to prove it again or go through some formalities at the new place.
So, even if that certification doesn’t hop jobs with you, the cool skills and experience you’ve got under your belt make you a hot pick for employers looking for someone who knows their way around a forklift.
What to Do If Your Certification Isn’t Transferable
If your forklift certification doesn’t automatically transfer to your new job, here are some strategies to bridge that gap, with a bit more detail and some industry-specific lingo to get you up to speed:
- Pursue Additional Training: Sometimes, a short course or specific training module can update your certification to meet the new employer’s standards. For instance, if you’re certified on a Counterbalance forklift but the new job requires experience with a Reach Truck, you might need a few hours (let’s say 4-6 hours) of hands-on training to get up to speed. This is akin to upgrading software on your computer to make it compatible with new applications.
- Clarify Certification Requirements: Before you even accept a new position, have a detailed discussion with your potential employer about their certification requirements. Ask about the specific models of forklifts (e.g., Class I Electric Motor Rider Trucks vs. Class V Internal Combustion Engine Trucks) and the Occupational Safety and Health Administration (OSHA) standards they adhere to. Understanding the exact OSHA standard (like OSHA 1910.178) can clarify what additional certifications or endorsements you may need.
- Seek Bridging Courses: Some training providers offer bridging or refresher courses that are specifically designed to fill in the gaps between different certification standards. For example, if your certification is from a program that meets the ANSI/ITSDF B56.1 standards but your new job follows a more stringent ISO 3691-1:2011 standard, a bridging course can help align your skills with the ISO requirements. These courses typically range from a single day to a week (8 to 40 hours) and focus on both theoretical knowledge and practical skills.
- Obtain Recertification: If there’s no way around it, obtaining recertification under the new employer’s preferred training program might be necessary. While it may seem like starting over, this process ensures you’re fully compliant with the specific safety protocols and operational procedures of your new workplace. The recertification process could involve both written and practical exams, covering topics from load handling and equipment maintenance to workplace safety and emergency procedures. Depending on the complexity of the forklift operations and the regulatory environment, this could entail anywhere from 8 to 40 hours of training.
In the world of forklift operations, staying adaptable and continuously updating your skills and certifications is crucial. Always approach your certification with the mindset of lifelong learning, aiming not just to meet the minimum legal requirements but to exceed them for the safety of yourself and those around you.
Ready to Rev Up Your Career with Forklift Certification?
Get Certified Online & Be Job-Ready Today! It’s Fast & Easy!
With our online course, getting certified is as easy as clicking, learning, and succeeding.
Don’t let another day go by without taking the next step in your career.
You Need To Be Recertified When Transferring To A New Company
When you’re switching jobs and landing at a new company, you gotta get re-certified to drive a forklift, and here’s the lowdown on why that’s not just a bunch of red tape:
- New Rulebook: Think of it as switching from playing a video game on easy mode to suddenly playing on hard mode. The new place might have a 10-page safety manual instead of the 5-pager you’re used to. Every company has its own set of rules (like how fast you can drive the forklift or how high you can stack things) to keep everyone safe and sound.
- Safety First: Now, imagine you’ve always played soccer in sneakers, and suddenly you’re told you need cleats. New company, new safety gear, and rules. They might require you to wear different protective gear (like hard hats that can withstand a 5-pound object dropping from 10 feet up) or follow stricter safety protocols (like always having a spotter when moving loads that block your view).
- Different Workplace Hazards: Or, in real life, new workplace hazards. If your old job was all about navigating a warehouse full of paper products (think soft landings), the new gig might have you dodging around sharp metal parts or chemical containers. Different beasts, different dangers. You need to know the lay of the land, which could mean understanding how to operate in tighter spaces with less than a foot of clearance on either side or how to handle hazardous materials without turning yourself into a human glow stick.
- Different Forklifts: Finally, the forklifts. You might be a wizard on a stand-up reach truck, but what if the new job needs you to hop into a sit-down counterbalance forklift or, heaven forbid, a side loader? These machines can have wildly different controls, weight limits (like being certified to handle up to 5,000 pounds when you’re used to 3,000), and operating quirks. It’s like jumping from driving a sedan to maneuvering an 18-wheeler. You need the know-how to handle these beasts safely.
So, getting re-certified isn’t just jumping through hoops. It’s about making sure you can handle the new game with its own set of challenges, from the rulebook and safety gear to the monsters you might face and the spaceships you need to pilot.
Undergo Additional Training That The New Employer Requires You To Take
If your new job asks you to get more training, think of it as a good chance to get better at what you do. You might need to learn how to drive a different kind of forklift or understand new safety rules that are important at your new place.
This extra learning is really just adding more tools to your skill set. Look for training that fills in what you need to know, especially if it’s about handling a forklift you’re not used to or following new safety steps. It’s also a great idea to get hands-on practice during your training.
This way, you’re not just reading about it or watching someone else do it; you’re actually doing it yourself, which is the best way to learn. Always ask questions if you’re unsure about something. It’s important to be clear on how things work, especially when it comes to being safe on the job.
After you’re done with the training, use what you’ve learned at work. Be confident but careful as you get used to any new machines or rules. Remember, learning new things is part of the job and helps you become even better at what you do.
New employers often require their forklift operators to undergo specific training to ensure they’re up to speed with the company’s operations, safety standards, and equipment. Here are some common topics and training areas:
- Company-Specific Safety Protocols: Every company has its own set of safety rules, based on the kind of work they do and the layout of their facilities. New operators might need to learn about emergency procedures, safety gear requirements, and how to report accidents or hazards.
- Equipment Operation: If the company uses different types of forklifts or material handling equipment that the operator isn’t familiar with, training will be required. This can include instruction on operating electric versus internal combustion forklifts, or specialized equipment like order pickers and pallet jacks.
- Load Handling: Proper techniques for lifting, moving, and stacking different types of loads are crucial. Training might cover how to handle unstable or oversized loads, work with racking systems, and perform accurate inventory management.
- Workplace Navigation: Operators need to be familiar with the specific layout of the new workplace. This includes understanding traffic flow, pedestrian areas, loading docks, and any areas that require extra caution.
- Legal and Regulatory Compliance: There may be specific local, state, or federal regulations that operators need to follow. This could involve training on environmental regulations, hazardous material handling, or compliance with Occupational Safety and Health Administration (OSHA) standards.
- Maintenance and Inspection: Knowing how to perform daily inspections and basic maintenance on forklifts is often part of the training. Operators might learn how to check for mechanical issues, ensure batteries are charged and maintained, and report problems that require professional repairs.
- Soft Skills: Communication, teamwork, and problem-solving are key skills for forklift operators. They may receive training on how to work efficiently with coworkers, communicate effectively in a noisy and busy environment, and resolve issues that arise during operations.
Each new job may require a mix of these training topics, tailored to the specific needs of the workplace and the equipment being used. The goal is to make sure every operator is prepared, safe, and efficient on the job.
To Finalize This
To wrap things up, forklift certifications aren’t always something you can take with you from one job to another. Every company has its own rules and the machines you’ll be working with can be different too.
But don’t let that get you down. If you find out your certification isn’t transferable, you’ve got options like getting a bit more training or talking to your new boss about what you need to do.
Remember, the skills and experience you’ve gained are valuable, and with a little effort, you can get set up and ready to go at your new job. So, always be prepared to learn and adapt, and you’ll keep moving forward in your career.